XEBEC Self-Adjusting Sleeve™
Prefixed Brush length is automatically projected and assists unmanned operation. Effective to eliminate human error, maintain optimal machining conditions and consistent machining quality.
Applicable equipment

Machining center

Combined lathe

Special machine

Robot

General purpose lathe with milling function

Drilling machine

Rotary tool
(electric)

Rotary tool
(pneumatic)
Tool schematic
It consists of a sleeve and a rack gear.
XEBEC Brush Surface is not included.
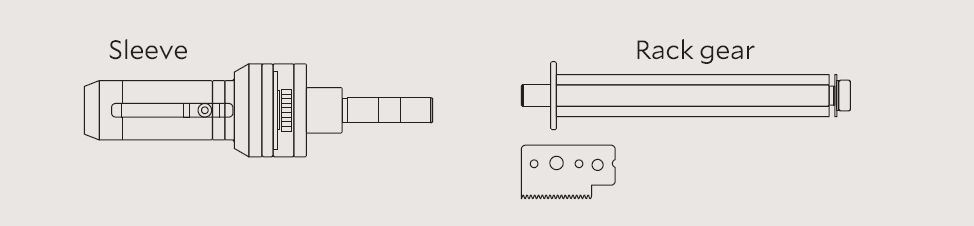
Sleeves
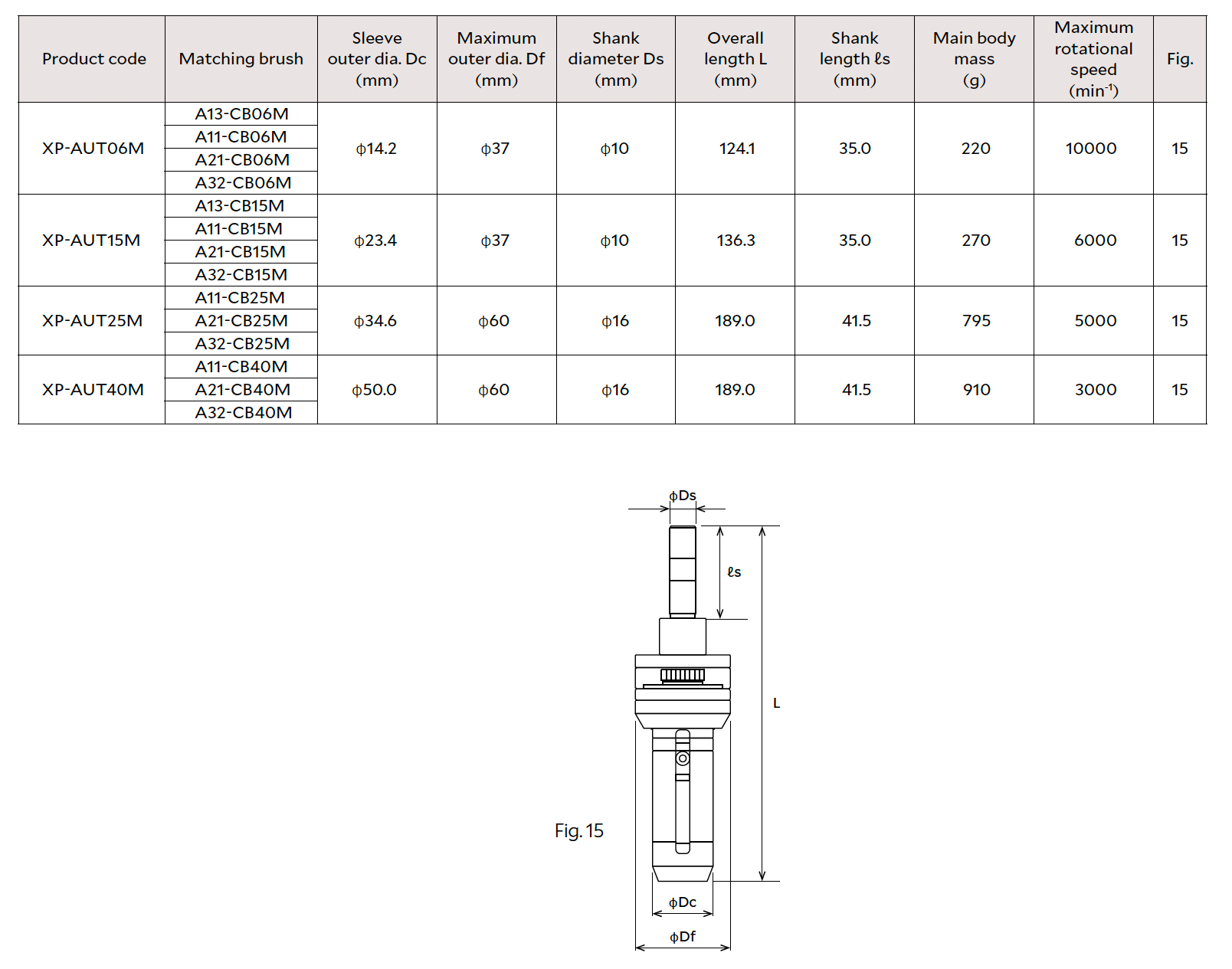
How to use
Applicable equipment
Self-Adjusting Sleeve must be mounted on the equipment which enables to stop and hold the sleeve at the fixed position.
Brush projection amount
Predetermined length can be adjusted between 0.05mm to 1mm in 0.05mm increments in a single action.
The projection amount is adjusted at the predetermined intervals according to wear volume.
How to decide projection adjustment cycle
1. Figure out the amount of brush wear by process quantity or travel length.
2. Set and execute the macro program so that the projection amount is adjusted at the predetermined interevals.
Example:
Deburring an aluminium part
Travel length: 200mm per workpiece
【Condition】
1. Brush wear: 2μm per workpiece
2. Brush wear: 0.2mm per 100 workpieces (Total travel length 20,000mm)
【Adjustment cycle】
Set the cycle to every 100 workpiece (0.2mm brush wear)
Example:
Finish processing of a cast-iron part’s edges
Travel length: 1,500mm per workpiece
【Condition】
Brush wear 50μm (0.05mm) per workpiece
【Adjustment cycle】
Set the cycle to every 1,500mm (50μm brush wear)
Recommended three operating patterns
This is a method to adjust only the part that is worn out by one-time processing immediately after processing.
By passing the side gear of main body through the rack gear immediately after processing, the brush projection amount is reset to the initial condition.
This is a method to adjust the cumulative wear volume generated by several processing at once.
By passing the side gear of main body through the rack gear once every several processing, the brush projection amount is reset to the initial condition.
This is a method to measure the brush wear volume using the sensor inside the machine and adjust only when a certain amount is worn out.
After processing, the sensor inside the machine measures the brush wear volume and decides whether adjustment is necessary. If necessary, the brush projection amount is reset to the initial condition.
Advantages and disadvantages of three operating patterns
Pattern 1: one-time processing/one-time adjustment
No minimum wear volume (wear volume: less than 50um/per time).
It might be possible to shorten the cycle time of pattern 1 (Every-time projection adjustment is not necessary).
A complicated macro program is required. (A program which decides whether adjustment is necessary or not).
At least two counters are necessary.(for tool life and for judging projection adjustment) .
Recognition of the wear volume in advance is necessary.
(The wear volume is a predicted value)
Pattern 2: several-time processing/one-time adjustment
No minimum wear volume (wear volume: less than 50um/per time).
It might be possible to shorten the cycle time of pattern 1 (Every-time projection adjustment is not necessary).
A complicated macro program is required. (A program which decides whether adjustment is necessary or not).
At least two counters are necessary.(for tool life and for judging projection adjustment) .
Recognition of the wear volume in advance is necessary.
(The wear volume is a predicted value)
Pattern 3: one-time processing/one-time measurement and occasional adjustment
Accurate projection adjustment based on measurement is possible.
Only one counter is required (for tool life)
Recognition of the wear volume in advance is not necessary.
No minimum wear volume (wear volume: less than 50um/per time).
The sensor inside the machine is necessary.
Cycle time gets longer due to sensing.
Micro program for some points is necessary.
Illustrations of each three operating patterns
The following shows how three operating patterns will make an operation.
In the following, the target workpiece and the sensor inside the machine will appear in addition to the XEBEC Self-Adjusting SleeveTM and the auxiliary item, the rack.
Please check the arrangement as shown below.
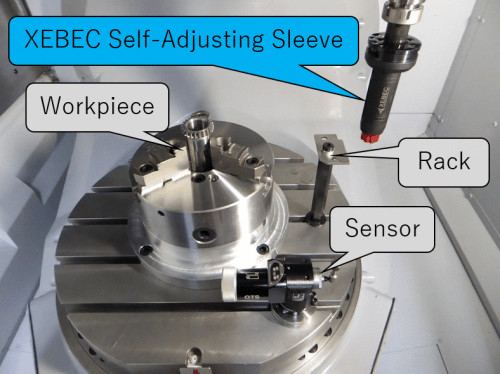
Pattern 1: one-time processing/one-time adjustment
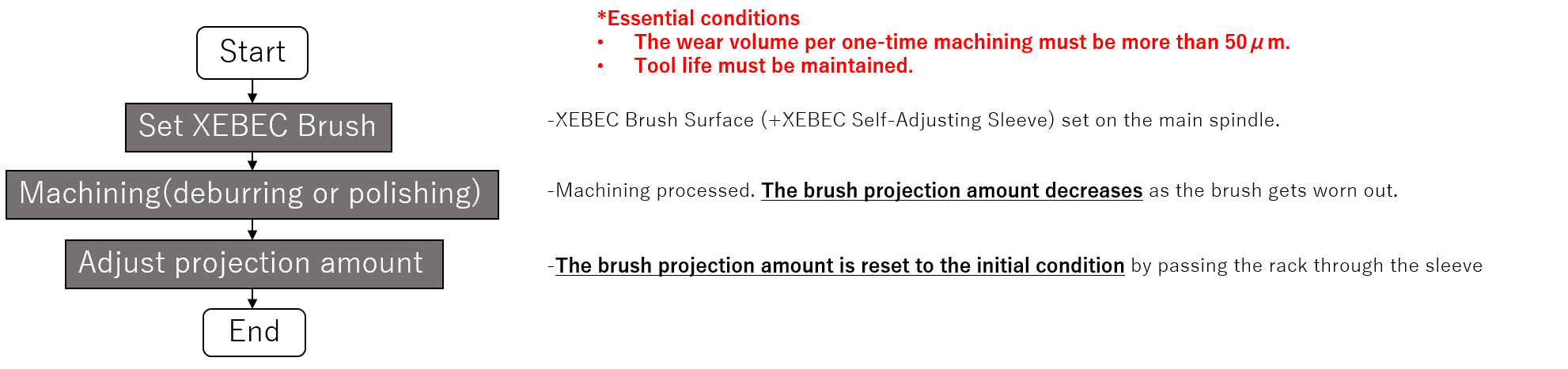
Pattern 2: several-time processing/one-time adjustment

Pattern 3: one-time processing/one-time measurement and occasional adjustment
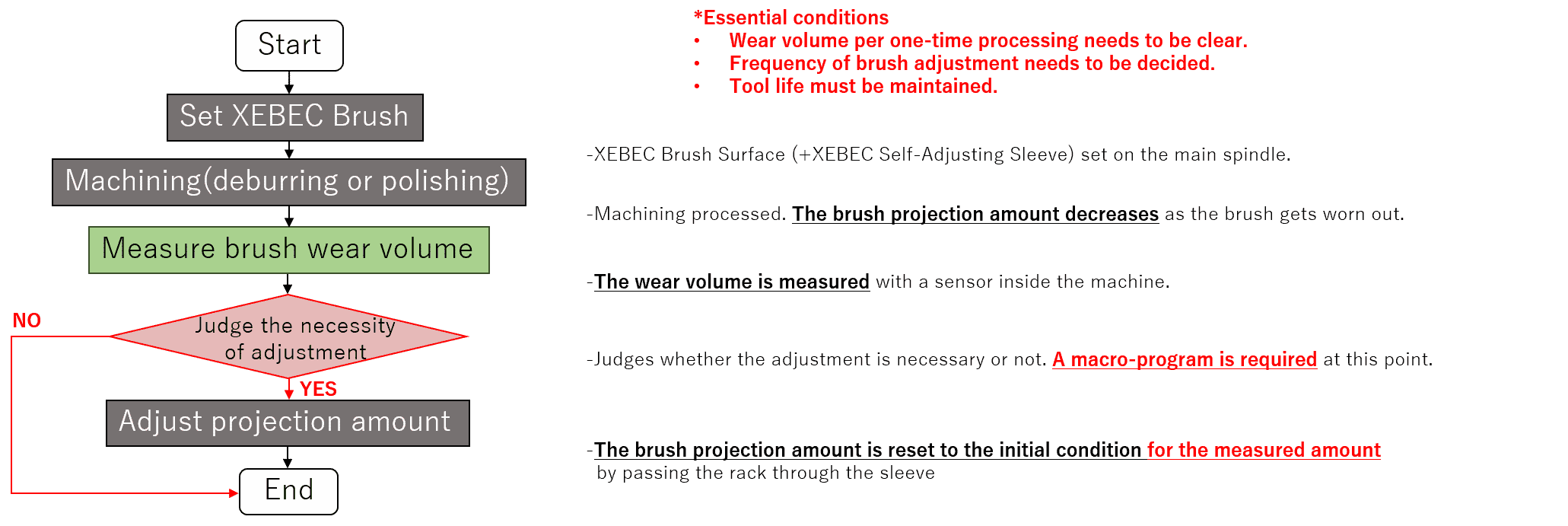
Maintenance
How to clean sleeve main body
*Recommended grease: Lithium soap grease (NLGI#2)
* Please confirm in advance that there is no deflection before use. Please confirm also that there is no loose screws, etc. after machining for a while.

